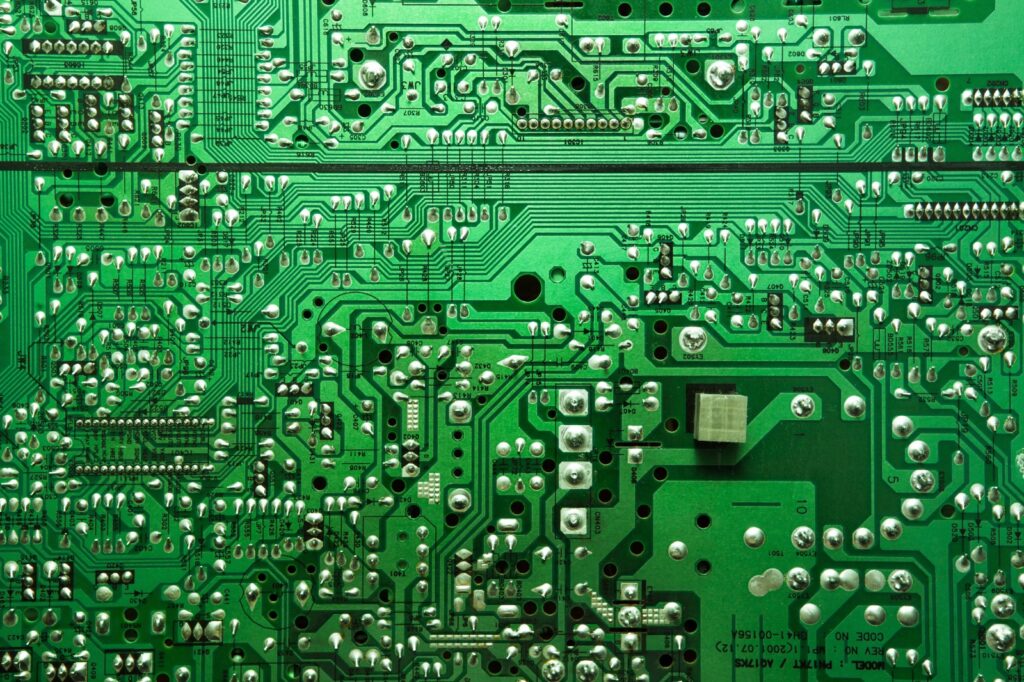
Resilience is the capacity to recover quickly. Basically, how you weather the storm. Today, we’re seeing new types of storms in the PCB industry unlike we’ve ever seen before, but our responses have been similarly flawed. So, diving deeper into the analogy of the storm, when you go to the supermarket to pick up toilet paper, they only have so much for a certain amount of time and then when a weather event occurs, the shelves are bare. This is very similar to what’s happening in the PCB industry. Our 20-year focus on hyper-efficiency has really led to hypersensitivity. Even smaller supply interruptions of “popcorn” parts can be a challenge.
When you talk about intelligence enabling resilience, it’s really the application of “outside-in” intelligence from across the electronics value chain that allows you to understand and reliably predict the weather. The earlier you can predict the weather, the earlier you can utilize that intelligence to make the right design decisions. So, it’s outside-in intelligence, it’s the ability to not only search for parts based on parametric information in your corporate library, but it’s the ability to access extended intelligence during those searches that include a leading indicator like “popularity”, for example. These represent parts that are the most popular based on patterns of new industry-wide design cycles. Or intelligence from searches that take into account diversity of alternatives, demand at time of design, and supply risk. So, if there’s a weather event, you won’t run out of toilet paper water or other necessities. Matter of fact, you’ll already be prepared because a risk alert would have lit up your smart phone before the actual event is even on radar.
How supply chain business challenges have evolved over time
The biggest problem back in the day may have been RoHS– meaning that you were just trying to make sure that your components met a specific requirement. It was also cost. Lead time was not the biggest challenge because you typically had enough leeway to do your design work, then send the initial Bill of Material over to component engineering to check for obsolescence and AVL compliance, and then onto the sourcing team to have them procure. Those days are over. Now, lead time, availability, and even counterfeiting are becoming huge issues.
When we first started designing PCBs, even sharing information was different because we barely had computers that were attached to a network and, therefore, sending data electronically was not as important as it is today. We must share electronic information a little bit differently, not just exporting out some format and then sending it over the wall, you need to have a cohesive and collaborative environment. We need to have more and more connected solutions because we have more and more connected devices that require more and more electronics. So, for example, my refrigerator now can tell me if I’m out of food.
Redesign is expensive. When a component engineer, or worse, a procurement professional, tells you, “I can’t get that part,” and you already spent weeks, if not months, designing and simulating the board, it becomes extremely expensive to rework.
The evolution of PCB design
Board designers and circuit engineers traditionally have had three competing perspectives they need to address simultaneously to be successful designing boards:
- Layout solvability. You’re solving to place and route your parts and connections in any circuit, whether it’s a standard or HDI, and mastering your CAD tool while you’re doing this.
- Then you have your signal integrity and performance.
- The third perspective is design for manufacturability. Is your board designed for producibility? It’s easy to make one of something. Much harder to make hundreds of the same thing.
In the end, the goal is to take these three perspectives into consideration, and you’re going to have to make decisions where it’s a give and take to accomplish all three. In the end, your goal is to make revision one work. It’s tough if you are doing this, but you don’t have the insight to the component details from the supply chain. This is what we have been missing all along – part intelligence at the point of the design.
Real examples of supply chain issues
A customer we met with about six months ago explained to us that their supply chain problem wasn’t just ICs anymore, but now included “popcorn” parts: resistors, diodes, and capacitors. And this represented new challenges. One of the real-world examples that they shared was that they designed-in an IC that worked at a specific frequency. Unfortunately, that specific IC was not available anytime soon. Typically, you might search for something that meets that threshold but never exceeds, but in this example, they actually were able to qualify the same IC at a higher frequency speed grade and were able to procure that one more easily. So, design-for-lowest-cost isn’t the top consideration anymore, it’s what do we need to do to get revision one working that can ramp to volume on time? It’s balancing availability, costs, and design feasibility.
Another couple of examples are in the automotive industry. If you’ve gone out to try to buy a new vehicle, it can be very difficult right now. Behind the scenes some automotive companies are removing touchscreens from models. And other manufacturers are eliminating all their HD radios and their heated seats because they couldn’t get the right chips required for them to do the development.
Adapting to the new normal with expanded scope of intelligence
We are engineering in a new normal. To adapt, you now need push-button access to expanded intelligence, availability, pricing, comprehensive searchable parametric information, and models—a component digital thread that unites cross-functional organizations. We talk about digital threads within Nex geneering all the time. In EDA, we focus on the design digital threads that include ECAD-MCAD and verification, for example. but the component digital thread touches all of them and is an extremely important element. The component digital thread does not just include searchable electrical information or physical package parametrics that we extract and consume from content providers, but it’s also rich supply chain data that goes beyond what’s stored on enterprise systems.
As you’re selecting parts during the design process, you need to have that expanded intelligence at your fingertips. If a particular part doesn’t meet your cost vs. risk envelope, you need that same single source of supply chain intelligence to determine if there are alternates. You will also want to continually audit your design BOM and do a health check to see if you’re still meeting your price, availability, and risk rank. You may also want to be able to compare different parts — again, not just electrically but also at the supply chain intelligence level. So, as I mentioned earlier in the Mil-Aero example, a particular part might be available at a higher frequency, and another at a higher cost, but in terms of availability, it’s readily available. With that intelligence you can balance those trade-offs.
Another key piece of the intelligence is the active risk alerts. There may be time when something happens in the middle of the night and some impact of a geopolitical event or environmental issue is felt. Back to the weather analogy, you want an alert that says there’s a storm brewing and you need to prepare.
Today, there are plenty of tools out there that can take a Bill of Material and run an audit. But there are no out-of-the-box solutions that can connect all the stakeholders of the NPI process, for example, together with the same single source of supply chain intelligence. And this is what’s going to allow our customers to weather that storm and create the resilience to face any of the growing challenges of this normal or the next normal.
Work is currently underway at Nex geneering to enable this intelligence phase. In our next episode, we’ll dive deeper into the third phase of creating a resilient supply chain, which is optimization.